Induction Shrink Fitting
Most metals expand when they are heated. Induction shrink fitting is often used to heat and thermally expand parts to allow the insertion or removal of a mating component. Shrink fitting motor housings, heat shrinking gears to shafts, flanges to hubs and induction bearing heating are just a few of the common examples of shrink fit applications.

A specialty motor housing is heated to 400ºF for insertion of the stator. The heating coil is located inside the bore.
A bearing housing is heated using the coil shown for shrink fit assembly of the
components of a roller bearing.

The gear was heated to 600ºF in 15 seconds using a HS5000R2 heater and then slid onto the hub.

An internal heating coil is inserted into the shaft bore to expand it to attach the rotary fitting


The internal coil used to heat the housing. The coil assembly is molded in a thermally conductive epoxy for best fit in the bore.
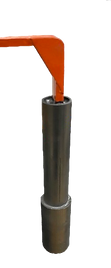

A long, cylindrical cast heating coil
is inserted inside a specialty motor housing to heat from the ID.
A DC motor head bore and rim are
heated at the same time for shrink fitting on the motor housing.


A large gear is heating for shrink fitting on to a shaft. The temp is controlled with a magnetic thermocouple